The selected work from PUNJAccelrator
Modular Robotics in Service Sector
(ME Design, IIT Ropar)
A broad perspective is presented for the utilization of modular robotic arms in various industrial tasks, particularly for cluttered environments. Parameters-based modules are proposed to develop reconfigurable manipulators according to the robotic parameters, resulting out of the design procedure.
Non-repetitive tasks to be done by a robotic manipulator in different cluttered environments requires variable attributes of a robotic arm. Conventional robotic arms with fixed configuration may not suffice of any random environment. However, Modular re-configurable manipulators fits best as the solution to this problem. For the given Task-Space-Locations (TSL) and a base point, a robotic arm can be configured using a set of modules as shown in Fig. 1. Modules are designed so as to be adaptable to all the Denavit-Hartenberg (DH) parameters. These modules can be assembled in series according to some assembly rules and geometric parameters can be altered in the modules itself to get a new configuration. To span the areas of application of modular robots, a modular library could be developed consisting of modular elements viz. link modules with different limits of adjustable lengths, end effector modules vary in types and sizes, actuator modules having a range of torque capacity, etc. Designing optimal sets of modular elements for the modular library, their assembly and control is considered as a challenge here. The set of modules chosen from the modular library to assemble an optimal configuration will depend upon the task-space where the manipulator has to work.
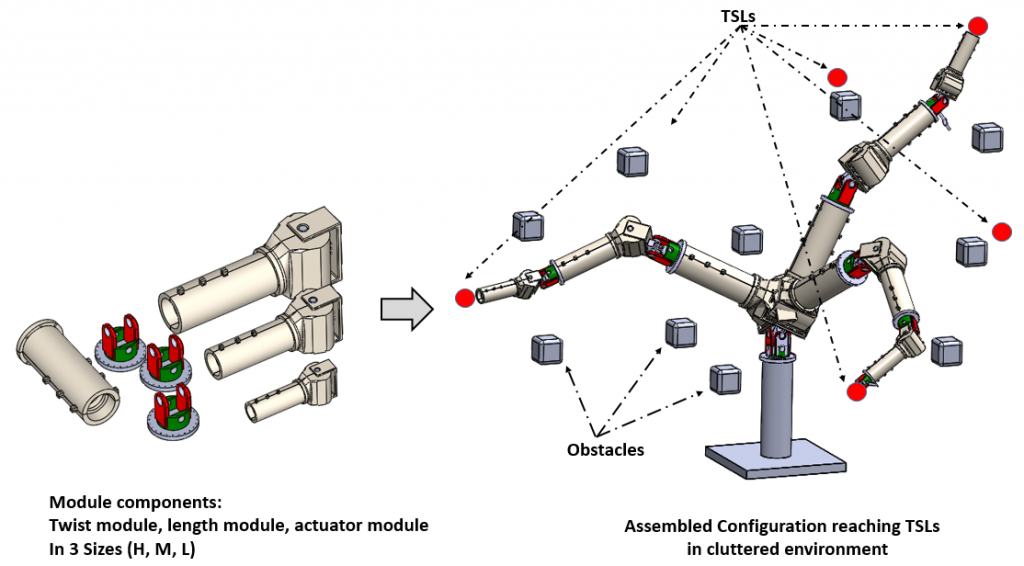
Environment Development in Customised Robot Design
(ME + CSE, IIT Ropar)
The exact construction of the manipulator’s environment and the boundaries is of significant importance because of its impact on manipulator design. A common approach of determining manipulator workspaces is geometric modeling. However, it is difficult and time-consuming to develop a geometric model of a cluttered environment. A framework is proposed for the automatic reconstruction of workspaces where a manipulator is required to function. Focus is also laid on reducing the size of the workspace model while preserving its geometric features. In essence, our work aims to reduce human intervention in designing manipulators. The framework is developed in the Robotic Operating System (ROS). The framework utilizes a depth sensor for generating data from the environment, which undergoes further processing to generate a mesh which represents the workspace.
Depth sensor in environment 1 depth sensor in environment 2 point cloud data of environment 1 point cloud data of environment 2 stl format of environment 1 stl format of environment 2
Generation, Evaluation and Dimensional Synthesis of Planar Hybrid Manipulators
(ME Design, IIT Ropar)
With the increasing variations in the robotic applications, there is more utilization of hybrid configurations for the design of robotic manipulators. The motivation lies in the fact that serially connected links generally selected for larger manipulability, and parallel manipulators do utilize for better positional accuracy. Common choices of hybrid configurations include either serially connected parallelograms or a loop inserted in a serial manipulator at different locations. With various hybrid combinations possible, even with a fixed number of degrees-of-freedom (dof), the experience and previous knowledge play key-roles in the selection of a basic configuration. Once a basic structure is selected, then it is followed by some systematic/optimal geometric synthesis, kinematic and/or dynamic design methodologies. However, selection of a basic structure of a manipulator configuration itself is critical enough, which needs attention.
The solutions for the selection of a hybrid morphology, performance analysis platform and optimal dimensional synthesis of planar hybrid manipulators, the work had been planned in four phases — random morphology generation, retrieval of kinematic information, unified performance evaluation criteria and evolutionary synthesis for planar hybrid manipulators. `Morphology’ here is referred to a basic kinematic framework for a manipulator. An extensive set of hybrid configurations are randomly generated for a range of number of degree-of-freedom and evaluated through a proposed unified approach for kinematic performance analysis. It provides a most suitable planar hybrid morphology selection for a given set of task-space locations.
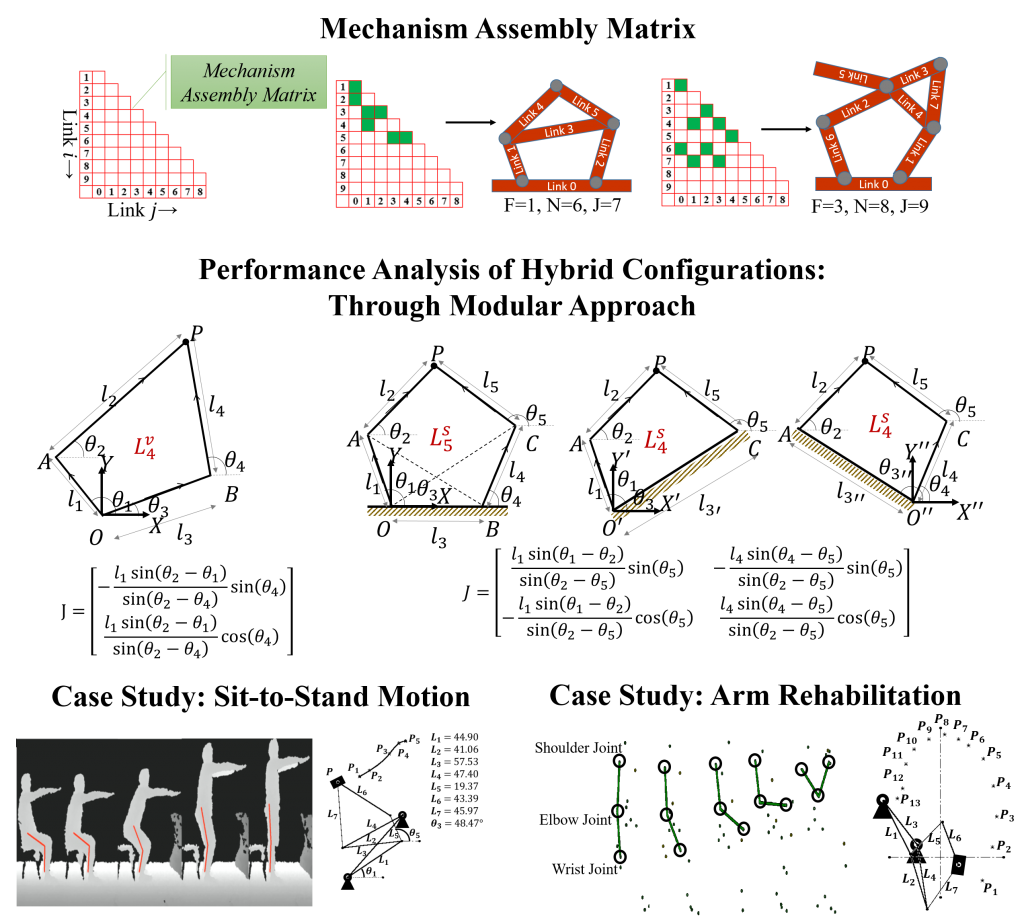
Task-Based Dimensional Synthesis and Modular Development of Wearable Upper-Limb Exoskeleton
(Manufacturing + Design Group, IIT Ropar)
Application of wearable exoskeletons are increasing in diversified fields, viz. soldiers/ workers for enhancing load carrying capacity, assisting stroke patients, paraplegics and spinal cord injured persons for rehabilitation purposes. Thus, robotics is designed to assist a user in such a manner so that user can enhance load carrying capacity or recover the movement of affected limb/ joint. This modified limb/ joint can be designed for upper limb, lower limb or both. The robotics which is designed for an upper limb is called upper limb robotics. This work is proposed to contribute in the area of wearable upper-limb exoskeletons that are designed and developed for rehabilitation applications. There are many design challenges faced by researchers such as anatomical alignment, length adjustment, centre of rotation, lightweight, high strength, and stiffness, human safety and comfort, etc. This work focuses on anatomical alignment, length adjustment, and modularity. The proposed work is categorized into three phases including task identification, task-based dimensional synthesis, and development of the modular library.
Inverse Kinematics of a Customized Surgical Arm
(CSIO ChD, IIT Ropar, TU)
The ongoing task is towards the inverse kinematics solution for redundant arms which can be used in real-time control.The increasing applications of robotic manipulation demand versatile manipulators which can work in cluttered environments of the industries. Relying upon the standard robotic arms is not appreciable and focus changes towards redundant manipulators which can manoeuvre through complex workspaces without much difficulty. The kinematically redundant manipulators which possess more degrees-of-freedom (dof’s) then required for the task, contribute to a great extent in collision avoidance, singularity avoidance and also in fault-tolerance. However, these advantageous extra dof’s come with the inherent problem of infinite solutions to inverse kinematics of the manipulator.
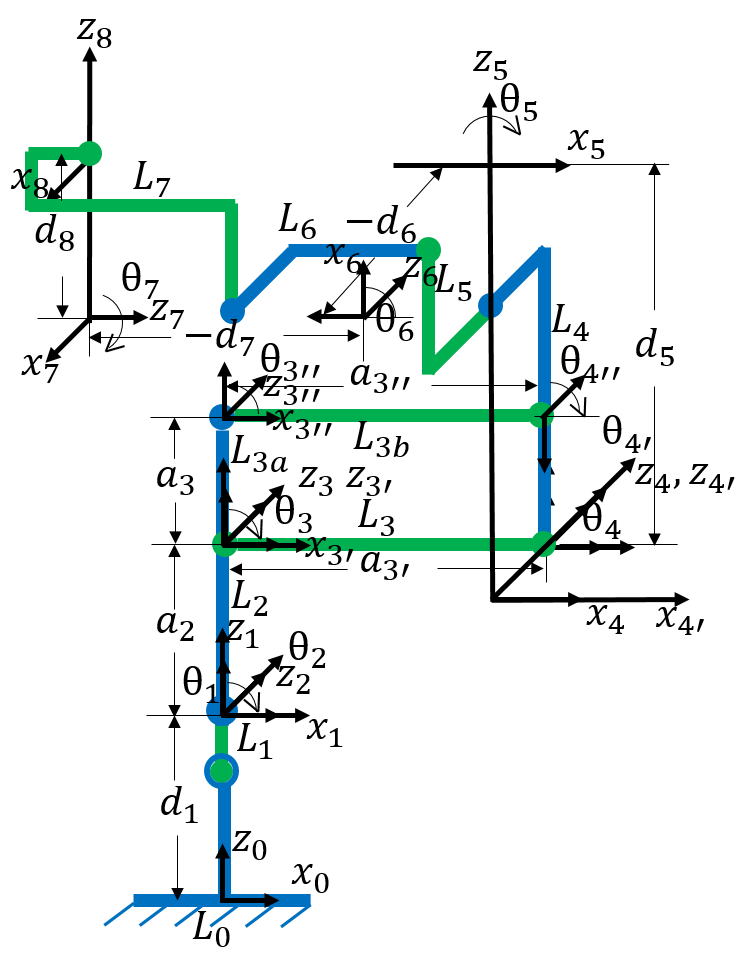
Artificial skin with pressure and strain sensing capabilities for robotic systems
(Mechanical + Materials, IIT Ropar)
With the application areas of robotic system is ever growing from security to medical to agriculture, there is a need to develop advance sensors which can allow robots to interact with surroundings in a better way. Our goal is to develop artificial skin with pressure and strain sensing capabilities. The primary requirement for such a skin will be that it should be flexible and exhibit desired resistance to external thermal and mechanical loadings. To this end, a novel artificial skin is being developed using advanced materials design concepts like functionally graded materials and carbon nanotube based hybrid and nano-composites. The first trial of artificial skin will consist of soft, elastic material filled with carbon nanotubes. The integrity of the developed skin with base robot material will be tested using multitude of experimental and computation tools
– Quadcopter (Mechanical, IIT Ropar)
– Robotic Manipulator for Nuclear applications